9 Advanced Planning and Scheduling Benefits for Your Manufacturing Facility
Keeping production smooth is crucial for manufacturers, especially as they face the challenges of growth and diversification. Dealing with unexpected machine breakdowns, large surprise orders, or parts shortages can significantly disrupt operations. Understanding the advanced planning and scheduling benefits becomes essential in navigating these challenges effectively.
Keeping production smooth is crucial for manufacturers, especially as they face the challenges of growth and diversification. Dealing with unexpected machine breakdowns, large surprise orders, or parts shortages can significantly disrupt operations. Understanding the advanced planning and scheduling benefits becomes essential in navigating these challenges effectively.
But how do you manage all these variables and swiftly adapt to surprises to meet customer demands?
Implementing an APS system offers a strategic solution, directly addressing these concerns to maintain seamless production. This approach is particularly beneficial for smaller manufacturers with limited planning resources, simplifying the task of integrating all critical factors into the planning and scheduling process.
Read on and discover how APS operates and assists manufacturers in keeping their production lines running smoothly and at full capacity.
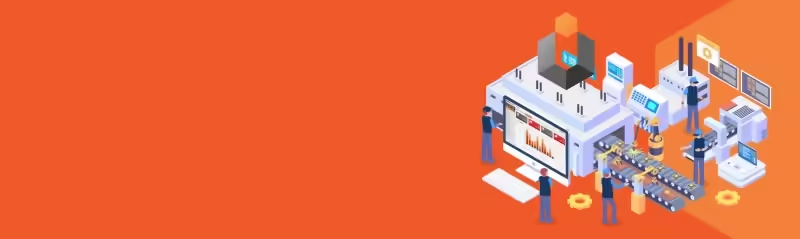
What’s Advanced Planning and Scheduling (APS)?
Advanced Planning & Scheduling (APS) is a software tool designed to improve the efficiency of capacity planning, production scheduling, and material requirements planning (MRP), working in conjunction with your existing ERP system.
It differs from traditional planning methods by using real-time data, complex algorithms, and optimization techniques to support decision-making that aligns with the company’s strategic goals.
APS Use Case
Imagine a custom plastics product fabricator that turns raw materials into automotive parts. Without Advanced Planning and Scheduling (APS), they might rely on manual planning, using past sales and basic forecasts. This approach could cause issues like overstocking materials for products that aren’t selling, not having enough capacity for in-demand items, or facing delays in shipping orders.
By adopting APS, the fabricator can tap into a sophisticated software solution that examines critical data points such as current inventory levels, the capacity of manufacturing equipment, supplier delivery timelines, and shifts in customer demand. The APS system then creates optimized production schedules, ensuring the right resources are allocated where needed, production goals are met, and orders are delivered on time.
In this scenario, APS empowers the fabricator to take control of its operations with a data-driven strategy for planning and scheduling. It allows them to adapt to changes in market demand, supply chain hiccups, or machinery malfunctions, leading to a smoother and more efficient manufacturing process.
Advanced Planning and Scheduling Benefits
By integrating an APS with existing enterprise resource planning (ERP) systems, manufacturers can achieve numerous benefits that streamline operations and significantly boost overall business performance.
Improved Production Planning
APS systems enable more accurate and detailed production planning by considering a wide range of variables, including machine capacity, labor availability, material requirements, and delivery schedules. This comprehensive approach ensures that production plans are both realistic and optimized, reducing the risk of bottlenecks and ensuring that resources are allocated efficiently.
Increased Production Efficiency
By optimizing production schedules, it helps to minimize setup times, reduce changeovers, and improve machine utilization rates. This leads to increased throughput and higher productivity levels, as production lines can operate more smoothly and continuously.
Improved Supply Chain Coordination
APS systems enhance coordination across the entire supply chain, from suppliers to customers. By providing real-time visibility into production schedules, inventory levels, and demand forecasts, these systems enable better collaboration and synchronization among all supply chain partners, reducing lead times and minimizing the risk of stockouts or excess inventory.
Better Customer Service
With APS, manufacturers can provide more accurate delivery dates to their customers and respond more quickly to changes in demand or custom orders. This improved responsiveness enhances customer satisfaction and can lead to stronger, more loyal customer relationships.
Improved Financial Performance
The efficiencies gained from implementing an APS system can directly impact a company’s bottom line. Reduced inventory costs, increased production efficiency, and improved customer satisfaction all contribute to higher sales and profitability.
Full Visibility and Control
APS systems offer unparalleled visibility into every aspect of the production process, from raw material availability to the status of finished goods. This complete overview enables managers to make informed decisions quickly, adjust plans as needed, and maintain control over their operations.
Increased Utilization and Leaner Operations
By precisely scheduling production activities and minimizing waste, APS systems support lean manufacturing principles. This leads to more efficient use of resources, reduced waste, and lower operational costs, making the entire manufacturing process more sustainable.
Faster Response to Change
The dynamic nature of APS systems allows manufacturers to quickly adapt to changes, whether they are shifts in market demand, supply chain disruptions, or internal production issues. This agility is crucial for maintaining competitiveness in today’s fast-paced business environment.
Higher Margins
By fine-tuning production efficiency, elevating customer service levels, and minimizing expenses, your manufacturing operation can achieve a more advantageous cost structure. This strategic approach not only simplifies operations but also leads to greater profit margins in a professional manner.
Final Thoughts on Advanced Planning and Scheduling Benefits
Final Thoughts
Embracing Advanced Planning and Scheduling (APS) is more than just an operational upgrade-it’s a strategic move that empowers manufacturers to navigate today’s complex production landscape with confidence. By integrating real-time data, optimizing resource allocation, and enhancing supply chain coordination, APS delivers measurable benefits: increased efficiency, leaner operations, and improved customer satisfaction. The ability to adapt quickly to change and maintain full visibility over every aspect of production ensures your facility remains agile and competitive.
Enhance Your Manufacturing Schedule with INDUSTRIOS APS
Adopting INDUSTRIOS APS for your manufacturing operations unlocks a myriad of advantages:
- Takes planning to the next level by considering machine capacities, workforce availability, material needs, and delivery schedules, leading to harmonized and efficient production plans.
- Quickly adjusts schedules in response to unexpected events, ensuring operational efficiency even amidst manufacturing’s inherent unpredictability.
- Streamlines the allocation of machinery, labor, and materials by utilizing simulations for predictive insights, enhancing efficiency, reducing costs, and shortening lead times.
- Enhances communication and collaboration with a comprehensive view of the manufacturing process, facilitating coordinated planning among production, sales, and supply chain teams.
- Secures a significant competitive edge with precise, flexible, and efficient scheduling processes, improving response times to market changes, reducing lead times, and ensuring superior product quality for sustainable growth and profitability.
Learn more about APS scheduling and its benefits in one of our latest IndustriOS blog posts. Keep your operations efficient with the latest industry insights. [Read More]
Request a Demo
Explore the full potential of IndustriOS software in elevating your manufacturing floor’s productivity. Schedule a consultation with our IndustriOS experts to gain a deeper understanding of our solutions and how they can be tailored to meet your specific data and technology needs.
[Get Demo]