Full Inventory Count: A 3-Part Guide on How You can Excel Your Inventory Management
In the first part of this 3-part series, we covered the basics of physical inventory counting including the types of counts and their benefits. In this post, we’ll dive deeper into one of the main counting methodologies—full inventory counts.
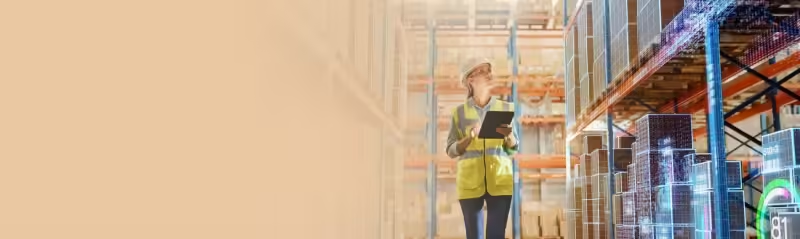
What is a Full Inventory Count?
A Full Inventory Count is the process of counting, verifying, and inspecting the entire inventory of a business at a specific interval (i.e. annual or biannual). This tried-and-true method involves physically tallying and examining each item in stock, comparing the results of the physical count against the amounts recorded in the Inventory System, and reconciling any discrepancies.
Oftentimes, performing a Full Inventory Count requires a business to suspend its operations during the count, and a significant amount of time and effort is required to complete the process, even when utilizing Electronic Counting Methodologies. However, this method does ensure higher levels of accuracy, as may be required for compliance by some regulatory bodies and allows a business to reset and refresh their inventory records.
When You Should Perform a Full Count
Full inventory counts are typically performed on an annual or biannual basis. The specific timing should be chosen to minimize disruption to business operations as much as possible. Many companies opt to perform counts after peak seasons or slow periods.
How to Perform a Full Inventory Count in 6 Easy Steps
Proper planning and preparation are required to maximize the success of a Full Inventory Count. Take a closer look at the following step-by-step guide on how you can perform a full inventory count:
Step 1: Set the Date
- Set the date(or dates) for counting in advance, with emphasis on selecting a time frame. that minimizes the impact on business operations.
- Notify all employees and parties involved well in advance.
Step 2: Create ‘Counting Teams’
- When determining who will perform the counting, it is ideal to assign two-person teams.
- Clearly identify the counting duties of everyone involved.
- Each team should have one person assigned to counting, while the other records counts manually or electronically
- Prepare all of the necessary tools for counting in advance and ensure that the people involved in counting and recording are properly trained in how to use the tools at your disposal.
- Ensure the counters and recorders are properly trained on how to use the tools.
Step 3: Categorize Your Inventory
- Divide the inventory into manageable categories to assign to teams.
- Examples include: Item Type, Locations, Bins, value, usage.
- You can also Prioritize the items that are most valuable and/or fast-moving, by utilizing an ABC analysis method.
Step 4: Pre-Count Logistics
- After breaking down your inventory into appropriate groupings, assign lists to each team and set deadlines for each category.
- Use a warehouse map to optimize distance and routing for counting teams.
- Freeze all warehouse activities at the time counting starts.
- Stop all deliveries to and from the warehouse.
- If necessary, segregate any newly received or outgoing goods to avoid counting.
Step 5: Counting Methods
- As counts are completed, compare physical totals to system totals
- If there are any items that are difficult to count, like liquid or bulk materials, it is recommended to use an estimation method based on weight or volume.
- As counts are completed, compare the physical count with the system count and record any variances.
Step 6: Post-Count Analysis
- Your IndustriOS Inventory System will compare physical count quantities with the recorded quantities and generate a variance report, for review.
- Investigate and correct any significant discrepancies.
- Adjust inventory records accordingly.
- Possible causes of discrepancy include misplacement, misclassification, damage, theft, data entry errors, and even miscounting.
- When completed, review and analyze the Full Inventory Count to identify trends or patterns that indicate erroneous behaviors or inefficiencies in the inventory process.
- Implement changes for future counts.
Do you like this article? If so, we’ve got plenty more engaging and informative content for you to explore. Click on any of the following links to dive into more of our blog posts:
[List of internal links to other IndustriOS articles]
What are the Pros and Cons of a Full Inventory Count?
Performing a Full Inventory Count can be a stressful time for everyone involved. Especially if you do not have the proper plan and systems in place to support your count, or if your team has not been sufficiently trained and prepared. Your IndustriOS Professional Services team can be an invaluable resource for advising on best practices for designing a successful counting plan, coordinating the process, & training your team to achieve the best possible outcomes.
Full Inventory Count Advantages
The biggest advantage of a Full Physical Count is that it delivers an exhaustive snapshot of your business’s inventory at a specific time. Also, a Full Inventory Count offers the opportunity to reset and refresh your inventory records, while identifying areas of risk and areas for improvement in your business processes. Additionally, if properly executed, it should satisfy any regulatory requirements a governing body may require of your business in regard to your inventory, allowing your business to remain compliant.
Full Inventory Count Disadvantages
The primary disadvantage to performing a Full Inventory Count is the amount of time and effort required to perform the count, wherein operations typically need to be suspended. Additionally, given that Full Inventory Counts typically happen infrequently, errors that occur after the count may go undetected until the next scheduled count. However, performing regular Cycle Counts after a Full Inventory Count has been completed can mitigate issues and concerns about errors that occur after the Full Count is completed, reducing the amount of time required for detection.
Final Thoughts
A full inventory count involves physically tallying and verifying every item in stock. It provides you with an exhaustive snapshot of inventory, but it requires you to stop your operations. Proper planning is key – set dates, create counting teams, categorize inventory, optimize logistics, compare totals, research discrepancies, analyze and improve. With enough planning and support, full counts will provide you with the value you need and minimal disruption.
With the assistance of your IndustriOS Account Services team, you will be able to institute a proper plan to execute a Full Inventory Count which is vital for mitigating the impact of performing this necessary procedure.
Stay tuned for our third and final blog about inventory counts where we’ll dive into cycle counts. If you missed the first one, then click HERE to learn more about everything you need to know about physical inventory counting.