AI-Enhanced Worker Safety: Reducing Accidents on the Shop Floor with Intelligent Systems
Discover how AI in production scheduling reduces delays, cuts costs, and optimizes resources for efficient manufacturing workflows.
The manufacturing sector is making strides in worker safety, with severe injuries plummeting from 8,943 incidents in 2023 to 2,856 in early 2024—a 68% drop driven by smarter risk mitigation. Traditional safety protocols, while foundational, often lag behind the split-second risks of modern production lines.
This is where AI-enhanced worker safety shifts the paradigm: instead of merely reacting to accidents, it identifies and neutralizes hazards in real time through predictive analytics, computer vision, and automated response systems. But what does it take to sustain this momentum and push toward zero preventable incidents with AI-enhanced worker safety at the core of every operation?
AI-Enhanced Worker Safety Key Takeaways
- Computer vision systems monitor real-time hazards like PPE non-compliance or proximity dangers, enabling immediate intervention.
- Wearable devices and IoT sensors track worker fatigue, environmental risks, and equipment health, preventing accidents caused by human or machine error.
- Immersive VR training simulates high-risk scenarios, improving hazard response and safety protocol adherence.
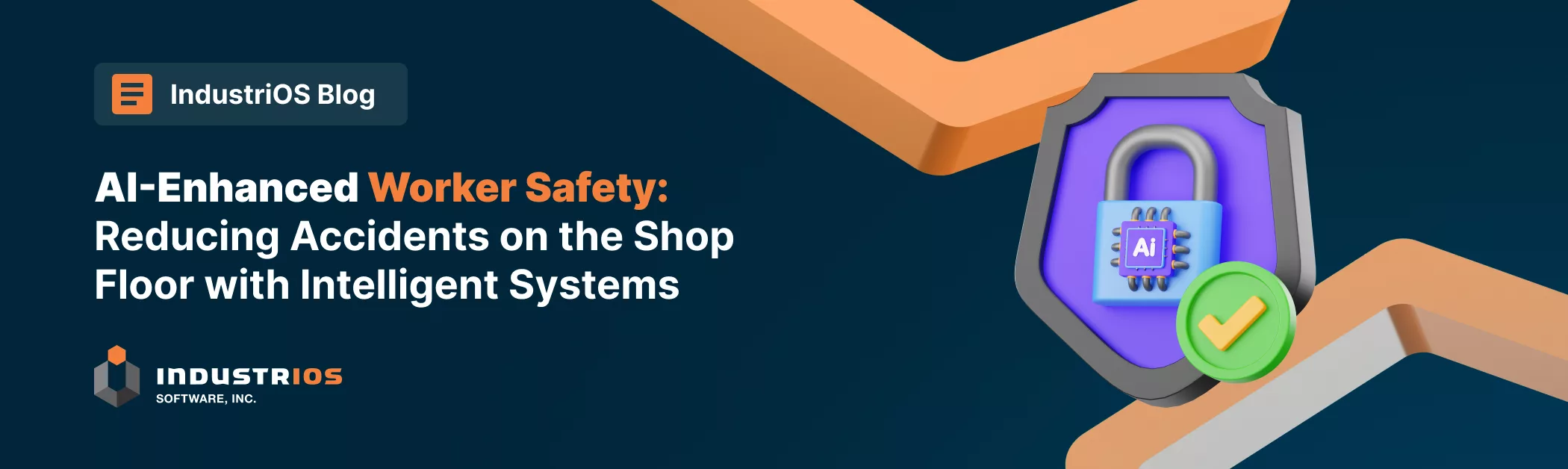
AI-Enhanced Worker Safety is a Multilayered Defense System
Modern manufacturing safety is an interconnected ecosystem where AI acts as both a shield and a sentinel. By integrating multiple technologies, these systems address risks at every stage, from prevention to response, creating environments where human expertise and machine precision work in tandem.
Anticipating Risks Before They Escalate
AI processes data from equipment sensors, workflow logs, and environmental monitors to identify patterns invisible to traditional methods. Machine vibration irregularities, repeated near-misses in specific zones, or shifts in worker movement patterns all feed into risk models.
These systems highlight not just immediate dangers but subtle trends, such as gradual increases in mechanical stress or airflow inconsistencies in confined spaces. Teams can then adjust maintenance schedules, redesign workflows, or upgrade equipment before minor issues escalate into critical failures.
Real-Time Monitoring with Computer Vision
AI-driven visual systems interpret context rather than passively recording footage. They distinguish between a worker momentarily entering a hazard zone and lingering unsafely, or detect improperly fitted protective gear instead of merely noting its absence.
Edge-based processing ensures immediate response—flashing warnings, slowing machinery, or sounding alarms—when sensors detect fatigue-related posture changes or unexpected overlaps between human and robotic activity.
This approach prioritizes situational awareness over surveillance, creating adaptive safeguards for dynamic environments.
Safeguarding Workers from the Ground Up
Advanced wearables now address industry-specific risks. Sensor-equipped gloves monitor grip strength during heavy lifting, while smart helmets track exposure to hazardous particles or noise levels.
Connected IoT networks link these devices to facility-wide systems, triggering actions like activating ventilation during chemical leaks or pausing conveyors if vital signs suggest heat stress.
This synergy between personal gear and environmental sensors tailors protection to both individual needs and worksite conditions.
Preparing Workers for High-Risk Scenarios
VR and AR simulations immerse workers in high-stakes scenarios without real-world consequences. Trainees troubleshoot malfunctioning equipment in virtual environments filled with sensory cues like alarms, visual warnings, and time pressure. Programs adapt to skill levels, challenging novices with basic shutdown procedures while veterans manage cascading crises.
Over time, AI analyzes performance gaps across teams, shaping targeted drills to reinforce weak areas and update protocols as risks evolve.
Balancing Innovation with Ethics and Practicality
Trust determines the success of AI safety tools. Privacy-focused design—such as anonymizing video feeds into abstract shapes or encrypting biometric data—helps workers embrace monitoring as protective rather than intrusive. Systems must also integrate seamlessly with existing machinery and workflows, avoiding solutions that demand costly overhauls or rigid procedural changes.
The aim is incremental improvement, not perfection, ensuring advancements respect both human dignity and operational realities.
INDUSTRIOS’ Role in Modern Worker Safety
INDUSTRIOS is exploring modular safety systems that could integrate IoT-enabled wearables, anonymized monitoring tools, and adaptive protocols. Our goal is to address real-time risks while maintaining productivity, and we are actively engaging with industry partners to refine these concepts.
We are committed to bridging the gap between legacy systems and modern safety demands through ongoing research and development.
Final Thoughts on AI-Enhanced Worker Safety
AI isn’t replacing human judgment—it’s augmenting it through AI-enhanced worker safety. Each layer of this framework reinforces the others: predictive analytics shape training scenarios, wearables inform risk models, and real-time monitoring refines safety protocols. Together, they create adaptive systems where prevention evolves alongside the workplace, empowering workers rather than replacing their judgment.
By integrating AI-enhanced worker safety into every layer of operations, businesses can transform shop floor dynamics and position themselves for long-term success.