Vendor Management: How to Select the Right ERP Software for Managing Approved Manufacturers
Learn how to choose ERP software for vendor management by assessing organizational needs, including vendor landscape, pain points, and compliance requirements.
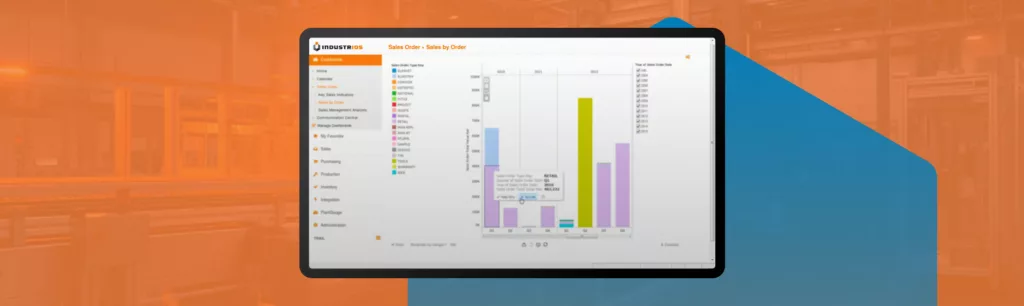
Managing relationships with approved manufacturers and vendors is essential for maintaining quality, compliance, and operational efficiency. The right Enterprise Resource Planning (ERP) software can simplify this complex task. This guide will help you navigate the selection process and identify key features needed for effective vendor management tailored specifically for the manufacturing sector.
Understanding Your Vendor Management Needs
Before exploring specific ERP solutions, it’s crucial to assess your organization’s unique requirements. Consider the following:
Current Vendor Landscape: How many approved manufacturers and vendors do you currently manage? Understanding the scale of your vendor network will help select a system that can handle your needs.
Pain Points: Identify your existing challenges in vendor relationship management. Are you struggling with compliance tracking, quality assurance, or communication gaps?
Compliance Requirements: What industry-specific compliance standards must your vendor management system meet? This could include certifications like ISO 9001 or U.S. Food and Drug Administration (FDA) regulations for specific industries.
Risk Assessment Methods: How do you currently evaluate and monitor vendor risk? Understanding your existing processes will inform how you need your new ERP system to function.
Key Features for Effective Vendor Management
When evaluating ERP software, look for features that specifically address the needs of manufacturers:
1. Vendor Database Management
A robust ERP system should provide centralized storage for vendor information. Look for features such as:
- Custom fields for tracking supplier certifications and compliance records.
- Document management capabilities to store important documents like contracts and quality reports.
- Historical performance tracking to evaluate vendor reliability over time.
2. Risk Assessment Tools
Effective risk management is critical in manufacturing. Your ERP should include:
- Risk scoring mechanisms to evaluate supplier risk levels.
- Automated alerts for compliance issues or performance dips.
- Custom fields to track financial health and assess the stability of suppliers.
3. Quality Management Integration
Quality assurance is vital in manufacturing. Ensure your ERP can:
- Track quality metrics relevant to your products.
- Manage non-conformance reporting and corrective actions.
- Provide audit trail capabilities to maintain compliance documentation.
4. Supply Chain Visibility
Real-time visibility into your supply chain is essential. Look for features that allow you to:
- Monitor lead times and track orders in real time.
- Integrate with inventory management systems to optimize stock levels.
5. Communication and Collaboration Tools
Streamlined communication with vendors can enhance efficiency. Consider:
- Integrated messaging systems for direct communication with suppliers.
- Vendor portal capabilities that allow suppliers to access relevant information easily.
- Document-sharing features that facilitate collaboration on projects or issues.
Considerations for Selection
When selecting an ERP system for vendor management, consider integration capabilities, scalability, user experience, and compliance features. Industrios ERP offers comprehensive solutions that address these key considerations while providing additional benefits for manufacturers.
INDUSTRIOS ERP excels in inventory optimization with features like supply management for on-hand, in-transit, on-order, and committed inventory, ensuring a clear picture of stock levels at all times. The system’s demand forecasting tools for buying items, making items, jobs, and minimums help manufacturers stay ahead of customer demand, addressing scalability concerns.
The software streamlines purchasing processes through advanced MRP calculations suggested requisitions, and time-phased ordering. User-friendly workbenches simplify shipping and receiving operations, integrating with logistics systems and utilizing barcode scanning for efficient inventory tracking. This focus on user experience enhances adoption and productivity.
INDUSTRIOS ERP’s cutting-edge consumption tools, including easy BOM (Bill of Material) creation and mobile barcode scanning for stock taking, further simplify inventory management. The system’s monitoring and analysis features, such as exception alerts, suggested minimums and maximums, and EOQ (Economic Order Quantity) calculations, provide valuable insights for informed decision-making.
By offering these comprehensive features, INDUSTRIOS ERP not only meets the core requirements for effective vendor management but also provides additional tools to optimize overall manufacturing operations and supply chain efficiency.
Implementation Best Practices
Successful implementation requires careful planning:
Define Clear Objectives: Establish what you want to achieve with the new ERP system, focusing on specific improvements in vendor management.
Data Migration: Prepare existing data by cleaning it up and ensuring it meets the new system’s standards. Plan how historical data will be integrated into the new software.
Training Programs: Develop comprehensive training programs tailored to different user roles within your organization, ensuring everyone understands how to use the system effectively.
Change Management: Communicate the new system’s benefits clearly across the organization. Address concerns proactively and involve key users early to encourage buy-in.
Common Pitfalls to Avoid
Be mindful of these common mistakes during the selection process:
- Overlooking Integration Needs: Ensure compatibility with existing systems and consider future integration requirements as your business evolves.
- Insufficient User Input: Involve end-users from various departments in the selection process to gather feedback on their needs and preferences regarding user interface design.
- Underestimating Training Needs: Plan comprehensive training programs that cater to different user skill levels, ensuring everyone is comfortable using the new system from day one.
How to Make Your Final Decision
To make an informed choice:
- Create a detailed list of requirements based on your assessment of needs.
- Request demos from top vendors focusing on scenarios relevant to your manufacturing processes.
- Check references from similar organizations that have implemented the software successfully.
- Evaluate the total cost of ownership, including implementation costs, ongoing support, and additional fees.
Final Thoughts on Vendor Management
Choosing the right ERP software for managing approved manufacturers and vendor risk is a significant decision that can greatly impact your organization’s efficiency and risk management capabilities. Focus on finding a solution that meets your current needs and future growth while maintaining strong security and compliance features.
Remember, successful implementation goes beyond selecting the right software—it requires careful planning, thorough training, and ongoing support to ensure maximum value from your investment. Take time to carefully evaluate options and involve key stakeholders to ensure the solution meets everyone’s needs.
- Reduce operational costs
- Improve overall efficiency
- Build stronger supplier relationships
- Respond more quickly to market changes
Manufacturers implementing AI-powered supply chain management will be best positioned to succeed in an increasingly complex global marketplace.
The future of supply chain management isn’t just about technology. It’s about creating more intelligent, responsive, and efficient systems that help businesses thrive in a rapidly changing world.