The Finished Goods Library is Always Open!
We have been publishing the Finished Goods since 2018 and the library is full of informative articles to help you get the most out of INDUSTRIOS. Check out the list of all past articles organized by processing area.
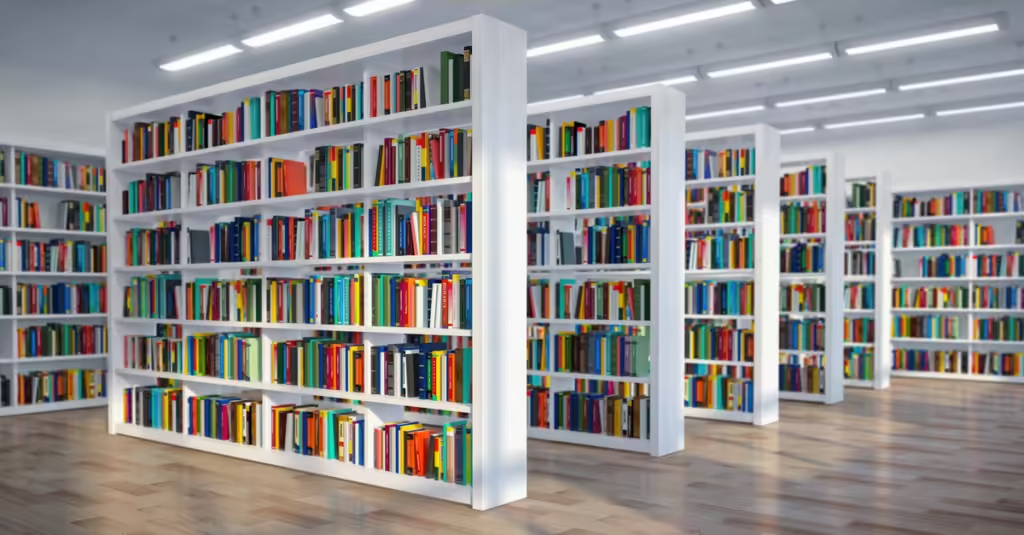
The library is also alway growing! Check back for new titles. Don’t see something you would like? Send an email to finishedgoods@industrios.com and we will add it to our list of future articles.
Inventory
- Inventory Master Keyword Search
- Calculate and Update the ABC Code
- Assign Serial Numbers by Scanning at Job Close
- Create Inventory Items During Sales Order Entry
- Multimedia in the Inventory Master
- Flexible Cost Details on the Inventory Activity Query
- Auto Assign Inventory Numbers
- Using Reason Codes for Inventory Adjustments
- How to Save a Range in the Inventory Activity Query
- The Direct Expense Cost Method – Track Quantities not Costs
- Minimums and Multiples for Selling Unit of Measure
- Where is an Inventory Item Used?
- Add New Inventory Items “On the fly” During PO Entry
- Dynamic Serial/Lot Numbers Using Tokens
- Did Someone Mention Stocking Units?
- Report Spotlight – The Aged Inventory Report
- Report Spotlight – The Inventory Valuation Report
- Group the Item Master from a Sales Viewpoint with the Sales Catalog
- Going Mobile with Inventory Queries
- Stay on Top of Item Audits with Appointments
- Report Spotlight – Inventory Distribution History Listing
- Report Spotlight: The MRP Action Report
- What’s Driving Suggestions to Expedite?
- Export the Inventory Activity Query to Support Targeted Analysis
- IOS 101 – The Benefits and Uses of the Non Stocking Inventory Item
- Simplify Item and BOM Maintenance by Using a Vendor Item Cross Reference
- Unfilled Material Requests – The Waiting for Inventory Workbench
- Close a Sales Order Kit to Inventory
Planning and Production
- IOS 101 – Material Planning and Suggested Orders
- The BOM Query – The “Where Used’ for Items and Phantoms
- Track Time and Materials to an Order Job
- Control Resource Assignment on Process Plans
- Manage Phase In/Out of Materials using BOM Effectivity Dates
- How to Re-Open a Closed or Cancelled Job
- How to Reassign Material to a Different Sequence
- Convert a Job to Requisition to Buy
- Allocate Overhead by Material Costs
- Convert Suggested Requisitions to Purchase Orders
- Add Notes to Labor Transactions
- Capture Reject Costs Mid Stream
- How to Flag Suggested Requisitions As Reviewed
- Visibility to Cancelled Job Costs on the Scrap Report
- Assigning Serial Numbers to Reworked Items
- Recording Time via Time Sheets
- Report Spotlight – The Job Status Report
- Report Spotlight – The Production Activity Report
- Report Spotlight – Labor Efficiency Report
- Prorating Shop Floor Time to Multiple Jobs
- The INDUSTRIOS Company Calendar and MRP Action Dates
- Alert Production to Changes in Linked Sales Orders
- Job Hold Reason Codes
- Save Time Closing Jobs with Saved Parameter Sets in Shop Floor Tracking
- Flexibility When Creating Jobs from Sales Orders
- Get Precise with Your Direct Labor Charges.
- Simplify Collection of Production Downtime
- Manage Production and Order Quantities Separately
- Voiding and Correcting Labor Transactions
- See the Full Picture when Manually Creating Subassembly Jobs
- Report Spotlight – The Work In Process (WIP) Financial Report
- Report Spotlight – Production Order Brief List
- Revalue Work in Process on Your Terms
- Be a Production Switch Hitter – Create a Purchase BOM from a Process Plan
- Answer Your Job Tracking Questions with the Enhanced Tracker Grid
- The Ins and Outs of Direct Purchase and Subcontract (DP/SC) Transactions
- IOS 101: Understanding the Impact of Lot Sizes
- Make Rework Visible and Then Tackle It
- Let Formulas Lend a Helping Hand
- Material Planning 101 – Expedite Days and the MRP Calculation
- Make Rework Visible and Then Tackle It
- How to Reassign Material to a Different Sequence
- Assign Serial Numbers by Scanning at Job Close
- The INDUSTRIOS Company Calendar and MRP Action Dates
Procure to Pay
- Receipts without Purchase orders
- Report Spotlight – Vendor Item Master Listing
- Quick Filters on the Receiving Query
- Track Changes to Vendor Promise Dates with the Promise Date Log
- Import a Vendor Price List
- How to Record In Transit Receipts
- How to Record a Vendor Deposit
- How to Use an Alternate Payment Vendor
- Get Out in Front of Vendor Lead Times
- Assign RMA Items to an External Resource
- Attach Receiving Documents to PO Receipts
- Adding Requisitions to Existing Purchase Orders
- Boost Purchasing Power with Blanket Orders
- Contract Purchasing – Part 1
- Contract Purchasing Part 2
- Identify the Internal Buyer on Purchases
- Set up and Track Recurring Vouchers
- Tying Up Loose Ends with Purchase Order Workflow
- Track Manual Workflow Changes with Activities
- Uncover Trends in Purchase Prices
- How are Your Vendors Performing?
- Email the PO Listing to Multiple Vendor Contacts
- Get Classy with Your Vendors
- Mandatory Fields on Purchase Orders and Sales Orders
- Quickly Focus on Open PO and SO Lines on the Inventory Activity Query
- Stay Current by Importing Vendor Promise Dock Dates
- Mix and Match – Consolidate Multiple Vendor Receipts onto a Single Voucher
- Keep Vendors in the Loop with Email Distribution
- Solve Missing Voucher Line Mysteries with Accrued Receipts
- The INDUSTRIOS Purchase Price Analysis Feature Helps Keep an Eye on Costs
- Rate Your Vendors on Timing and Quality with the Vendor Inspection Report
- Quick Filters on the Receiving Query
- Attach Standard Terms and Conditions to Outbound Emails
- Enlist the Sales Order Log to Track Changes to Sales Orders
- Manage Prospects and Customers Separately Using Account Types
- Limit Sale of Specific Items to an Approved List of Customers
- Use Customer Notes to Keep Account News Front and Center
- Use Sales Order Workflow to Quick Ship Items
- Automate Selection of Shipping Labels
- The Activity Log
- How to Consolidate a Bill of Lading
- Integrate an Approval into Your Workflow
Order to Cash
- Create Sales Order Kit at Quote Win Stage
- View Changes to a Customer’s Credit Limit
- Invoice Billable Only Lines – No Shipment? No Problem!
- How to Create a Price Book
- Import a Price Book
- Automate Selection of Shipping Labels
- Take Control of Shipment Sources
- Additional Dates for Sales Orders and Quotes
- How to Consolidate a Bill of Lading
- The Invoice Payment Customer
- Track Reasons for Debit Memos
- Tracking Salespeople on Sales Order Lines
- Drop Shipments for Everyone!
- Automatically Schedule Collection Calls
- Use Base and Mask to add Smarts to Default Revenue Account
- Add Replacement Items to Sales Orders Directly from the Bill of Materials
- Keep Your Team in the Loop with Workflow Notifications
- Integrate an Approval into Your Workflow
- Clear Invoice Numbers with Invoice Update Utility
- Creating and Copying Customer Service Tickets
- Add a Little Color to Customer Status
- Avoid Part Number Confusion and Use the Customer Item Cross Reference
- Let INDUSTRIOS do the Heavy Lifting in Planning Shipments
- Create Ship To Addresses Directly from the Sales Order Workbench
- Knowledge Transfer via Sales Order Notes
- Utility U: The Customer Mass Update Utility
- Report Spotlight – Customer Delivery Performance Report
- INDUSTRIOS Manufacturing CRM – Combining Customer Management with Operations Visibility
- Reassign Customer Deposits using Pre-Invoices
- New Certificate of Origin Requirements under CUSMA/USMCA/T-MEC Agreement
- Add a New Ship To On the Fly During Sales Order Entry
- Stay on Top of Receivables with the INDUSTRIOS Customer Collections Module
Sys Admin and Navigation
- The INDUSTRIOS Action Center
- Export Employee Data to Excel
- Expanded Linking of Appointments, Documents and Activities
- Control Viewing of Documents with the Document Type
- Spring Clean Your User Inbox
- How to Create a Diagram Dashboard
- User Parameter Sets on Wizards
- How to Create and Manage My Favorites
- How to Test Email Settings for IOS Users
- How to add a User Title and Signature to Custom Reports
- The Activity Log
- Who’s Who on Your Internal Team?
- Saving Time with Shortcuts in INDUSTRIOS
- Opening and Closing Periods in INDUSTRIOS
- Leverage Standard Text
- Write Back to User Tables
- Capture Rounding Issues with Financial Integration Partners
- System Admin Toolkit – Clearing Actioned Jobs
- Resending Emails in INDUSTRIOS
- Leverage the Application Server to Schedule Recurring Events
- Switch Things Up with INDUSTRIOS Themes
- Staying Productive When Working Remotely
- Take it Outside – Extend Analysis by Exporting Reports to Excel
- Balance Performance and Access with the Archive Product Group
- Safety and Savings are Always a Winning Combination
- Spring Clean Your User Inbox
PlantGauge and Dashboards
- Broadcast Important Safety Information Using PlantGauge Dashboards
- Keep an Eye on Shipment Values with a ‘Shipped Today’ Dashboard
- Boost Signals with a Color Coded Appointment Dashboard
- PlantGauge Dashboards Keep Key Measures Front and Center