Project Manufacturing 101: A study in adaptability
In any company that prides itself on custom work, it may be difficult to envision how anything can be standardized while still delivering the products and services customers depend on.
Project manufacturers must find a way to reframe their view of their projects and think about “how” they’re making versus “what” they’re making and look for those interconnected, repeatable elements.
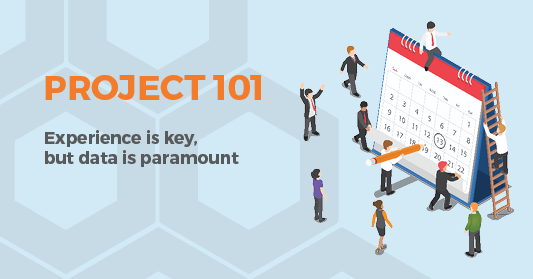
Project Manufacturing varies from traditional manufacturing in that one work week is typically different from the next. However, it’s important to recognize that there are common elements – processes, workflows, accounting practices, etc. – that benefit from a degree of standardization.
That’s where using the right enterprise resource planning (ERP) software can be a game changer..
The data collected from an intuitive ERP designed to work within a project-focused environment can do much more than help your accounting team eliminate redundant data entry into a swarm of pesky Excel spreadsheets. It will help identify repeatable tasks, commonly purchased materials and, most importantly, ample opportunities to reduce costs and improve margins on each job.
During a project or job, there is typically buying, manufacturing or fabrication, and other elements, all tightly scheduled against a project dates. Critical milestones must be met in sequence and on time to keep the project within budget.
A project-focused ERP allows you to define how you plan to supply all of a project’s demands. Management of advanced financial and supply chain elements goes beyond simple buckets of cost and time. Establishing budget buckets that accurately report costs versus spend along all aspects of a project provides more accurate forecasting, exposing areas of efficiency and leveraging them to turn a greater profit.
This brings us to budgeting. Every contract has an “external” budget – the amount that the customer agrees to pay. This figure is important to the customer, but it is also critical to profit. INDUSTRIOS ERP gives visibility to the integrated use of hours, materials and processes that define your profit margin against the job’s internal budget, indicating exactly how much negotiating room you have with the customer.